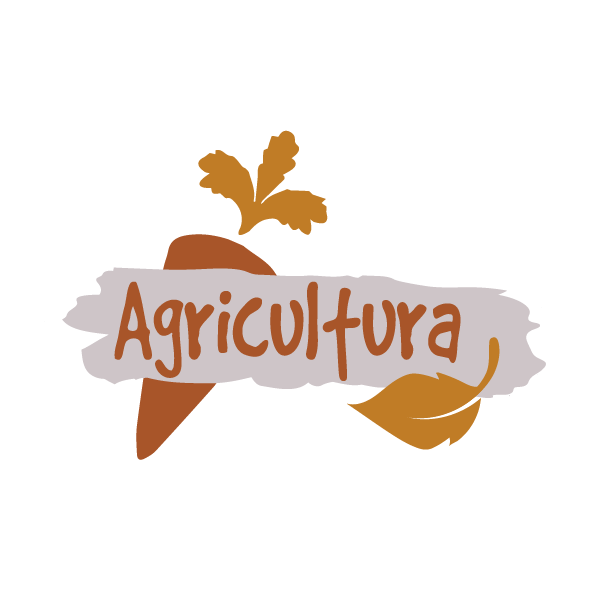
Aspectos técnicos relacionados con el riesgo de incendio en cosechadoras de cereales / F. Javier García
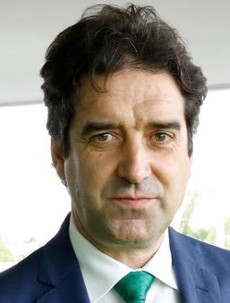
Fecha: 27-Nov-2019
Tags: incendios , maquinaria agrícola
F. Javier García Ramos
Departamento de Ciencias Agrarias y del Medio NaturalEscuela Politécnica Superior de Huesca - Universidad de Zaragoza
fjavier@unizar.es
La imparable evolución técnica de la maquinaria agrícola durante las últimas décadas tiene una de sus máximas expresiones en las cosechadoras de cereales, que representan la máquina “reina” de la agricultura de cultivos extensivos. Podríamos decir que son pequeñas fábricas sobre ruedas, capaces de realizar en una única pasada la siega, trilla y limpieza del grano para su carga en remolque o camión y posterior transporte a almacén.
Estas máquinas incorporan diferentes tipos de tecnologías: motores de gran potencia con sistemas de tratamiento de los gases de escape, regulación automática de los procesos de trilla y limpieza, sensores de rendimiento, motores hidráulicos para accionamiento de las ruedas motrices, sistemas de picado del residuo, cabezales de corte de gran anchura con diferentes tipologías, etc.
Sin embargo, cuando leemos en los medios de prensa (escrita, internet, etc.) la palabra “cosechadora”, suele ser en la época veraniega en la que se produce la cosecha de cultivos como el trigo y la cebada, y, en este caso, más que para hablar de las excelencias de este tipo de máquinas, encontramos noticias relacionadas con los incendios que han originado durante su trabajo en parcela. Y este hecho es una realidad que debemos abordar de forma objetiva y “con datos”.
En este sentido, según cifras del MAPA, en España, en los años 2017 y 2018, se han producido 13822 y 7143 incendios forestales, respectivamente, afectando a unas superficies totales de 178436 y 29907 ha. En relación con la causalidad del incendio, analizando la serie temporal del 2002 al 2015 los incendios originados por motores y máquinas representan el 3,18% del total. En el caso concreto de Aragón, en los años 2017 y 2018, se han producido 464 y 226 incendios forestales, respectivamente, que han afectado a 908 y 215 ha. Los incendios originados por motores y máquinas agrícolas han representado el 7% del total en 2017 y el 9% en 2018. Por lo tanto, los porcentajes de incendios causados por maquinaria agrícola se sitúan en cifras similares a las de los originados por causas naturales (rayo) que son significativas aunque muy por debajo, por ejemplo, de los originados intencionadamente (54% en España en el periodo 2002-2015).
Para centrar el problema hay que analizar las condiciones de trabajo de las cosechadoras. Las cosechadoras de cereal trabajan habitualmente con productos con muy bajo contenido en humedad (cereal apto para cosecha) y en condiciones ambientales de altas temperaturas que se pueden complementar con condiciones adversas de viento y humedad relativa. Es decir, trabajan en unas condiciones que pueden favorecer el inicio y propagación de un incendio si el material combustible (residuo de la cosecha) se pone en contacto con zonas calientes de la máquina. Para valorar el efecto de las condiciones ambientales se establecen diferentes índices de riesgo de incendio. Como ejemplo, en España, la página web de AEMET publica diariamente el índice de riesgo de incendio FWI (Fire Weather Index) para toda nuestra geografía. El FWI valora el riesgo de inicio de incendio y su posible comportamiento, a partir de la temperatura, el viento y la humedad de los combustibles. El nivel de riesgo se determina a partir de una escala con 5 categorías (bajo, moderado, alto, muy alto y extremo).
Centrándonos en la máquina, es recurrente la pregunta de si hay marcas o modelos que arden más que otros. Sinceramente, creo que nadie puede contestar a esta pregunta sin ser un osado puesto que las tecnologías utilizadas por los fabricantes son muy similares y existen factores adicionales que no dependen sólo de la tecnología (mantenimiento de la máquina, condiciones ambientales, utilización adecuada de la máquina, rendimiento de la cosecha, accidentes imprevistos, etc.) y que en la mayoría de los casos son determinantes. Lógicamente, se pueden relacionar algunos aspectos técnicos y de uso con un mayor o menor riesgo de incendio como por ejemplo: tipología del sistema de control de los gases de escape – EGR, SCR, salida libre-, potencia de la máquina, hectáreas trabajadas, sistema de ventilación de la zona del motor, aislamiento de los tubos de escape, etc.
Analizando con un mayor detalle los posibles puntos de origen del incendio en la máquina, las zonas de mayor riesgo son aquellas en las que la temperatura de las superficies de los diferentes sistemas y componentes es más elevada. Un reciente estudio realizado por el Laboratorio de Maquinaria Agrícola (LAMAGRI) de la Escuela Politécnica Superior de Huesca basado en datos correspondientes a una encuesta realizada en Aragón sobre un censo de 221 cosechadoras, de las que 74 sufrieron inicio de incendio, refleja que las zonas de mayor riesgo son: el motor y zona de salida de gases de escape (32 %), la barra de corte (31%), transmisiones y rodamientos (18%), fallos eléctricos (9%) y otras causas (11%). Estos datos son coherentes con los estudios existentes hasta la fecha (básicamente realizados en Australia y Estados Unidos) así como con datos de compañías aseguradoras, salvo discrepancias ligadas al dato de la barra de corte que es significativamente menor en los citados estudios.
En el estudio realizado por LAMAGRI se han monitorizado varias cosechadoras durante las campañas de recolección de 2018 y 2019, midiendo temperaturas de las principales zonas de riesgo. En todas ellas, como era de esperar, la zona con mayor temperatura ha sido el entorno del motor y la salida de los gases de escape. En la mayoría de los casos las temperaturas en esta zona se han mantenido por debajo de 160˚C, si bien es preciso reseñar que en algunas máquinas (aproximadamente el 20%) se han alcanzado temperaturas superiores a 250˚C, valor que representa el umbral de ignición para residuos de trigo y cebada de pequeña granulometría. También se han detectado temperaturas de hasta 400˚C en barras de corte mal mantenidas debido al rozamiento de la cuchilla con los dedos de la barra. Esta información permite cuantificar el riesgo de inicio de incendio de forma objetiva y, por lo tanto, facilita la toma de medidas para reducir al máximo las probabilidades de incendio.
Pero, ¿cómo cuantificamos de forma práctica el riesgo de incendio?. Cualquiera de nosotros, al hablar con un maquinista que ha sufrido un incendio hemos sido capaces de identificar el origen del mismo: “una chispa en la barra de corte”, “olor a quemado en la zona del motor”, “la bola o la aguja de un rodamiento que cae incandescente sobre el cultivo”, etc., pero hay que pasar de esas expresiones a datos objetivos con los que podamos valorar objetivamente el riesgo de incendio y plantear soluciones. Y estos datos objetivos son la medida cuantitativa de parámetros: la temperatura de la superficie de la máquina en sus diferentes zonas de riesgo, la temperatura de ignición del combustible (residuo de cereal) presente en el entorno de la máquina, el tiempo continuado durante el que la temperatura superficial de las zonas de riesgo supera la temperatura de ignición y las condiciones ambientales de trabajo (temperatura, humedad relativa, viento). Cuando se supere la temperatura de ignición en alguna zona de la máquina las posibilidades de inicio de incendio son elevadas y se magnifican si las condiciones ambientales son adversas.
Por otro lado, es preciso recordar que las cosechadoras tienen que trabajar en verano y que las condiciones ambientales de nuestras zonas “son las que son” en esta época del año, y difícilmente se van a tornar más benévolas. En este sentido, lo lógico es establecer medidas técnicas que reduzcan al máximo el riesgo de incendio antes que dejar las máquinas paradas en la nave. ¿A qué medidas nos referimos?.
Las medidas técnicas son variadas y pueden agruparse en cuatro niveles.
Nivel 1. Podemos considerar que este nivel es responsabilidad del fabricante y está ligado al diseño adecuado de la cosechadora para reducir el riesgo de incendio. Actualmente, se basa en aspectos como: aislamiento térmico de los tubos de salida de gases de escape del motor; utilización de materiales especiales en zonas sometidas a fricción como la base de la barra de corte; diseño de deflectores inclinados para reducir la acumulación de residuo; instalación de sistemas de ventilación y filtrado de aire en la zona del motor para evitar la acumulación de residuos; carenado del motor para evitar la acumulación de residuos; diseño de cribas de aluminio para reducir el peso y esfuerzo en los rodamientos; etc.
Nivel 2. La responsabilidad de estas medidas recaería principalmente en el usuario de la máquina. Este nivel representa las medidas por todos conocidas, ligadas a un correcto mantenimiento y uso de la máquina: realizar revisiones periódicas de las máquinas en taller homologado; cambiar rodamientos y cadenas de transmisión cuando cumplan el número de horas estipulado; ”soplar” el residuo presente en la máquina todas las mañanas antes del inicio de la jornada; revisar el correcto funcionamiento de la barra de corte y siempre parar y revisar la barra ante cualquier golpe con un obstáculo; no añadir a la base de la barra de corte aceros de alta dureza; utilizar como recambios piezas originales o avaladas por el fabricante; asegurarse de que los extintores manuales están en correcto estado; etc.
Nivel 3. Estaría constituido por la implementación de sistemas de monitorización que avisen del riesgo de incendio de manera objetiva mediante la medida en continuo de la temperatura de la superficie de las zonas de riesgo de la máquina, ligada a la medida en continuo de parámetros ambientales (temperatura, humedad relativa y viento). Este tipo de sensores representan un coste muy reducido respecto al precio de la cosechadora y permitirían, de una forma práctica, establecer avisos para la toma de decisiones del maquinista (reducción de las revoluciones de la máquina, incremento máximo de la vigilancia e incluso parada temporal de la cosechadora). En el futuro, también se podrían implementar otros tipos de sensores para la medida, por ejemplo, de vibraciones que indirectamente indiquen un incorrecto funcionamiento de transmisiones, rodamientos o partes de la máquina en movimiento.
Nivel 4. Como paso más avanzado las cosechadoras pueden ser equipadas con sistemas activos (hasta ahora hemos hablado de sistemas pasivos) de autoextinción cuyo uso no está extendido todavía en España, pero que ya se comercializan de forma habitual en América del Sur, Estados Unidos y Australia. Se trata de sistemas de extinción que aplican productos específicos para la extinción de incendios a través de una instalación fija con boquillas colocadas en diferentes zonas de la máquina, que se alimentan mediante un sistema de tuberías desde botellas/depósitos con producto antiincendios (polvo seco, líquido, duales). En base a información recopilada por sensores de temperatura u ópticos ubicados en las zonas clave de la máquina, capaces de detectar el origen del incendio, el sistema se activa automáticamente extinguiendo el mismo y evitando su propagación.
Como conclusión, aunque no es posible eliminar al 100% el riesgo de incendio originado por las cosechadoras, este tipo de máquinas no se deben demonizar. Aplicando medidas técnicas adecuadas basadas en la toma de información con sensores, realizando un buen mantenimiento y usándolas de forma profesional, dicho riesgo se puede reducir al máximo.